Anyone done any heat-management mods?
It's obvious that a lot of heat-induced wear&tear, degradation and mechanical failures take place in and around the engine bay of an e85 M54 engined zed and my leaky cam cover gasket is a testament to that fact- it was literally baked hard! I'm keeping an eye on the rearmost 2 coils too as these will be subject to higher temps than the forward ones.
As i plan to get another 100k miles from this car i'm thinking about some minor mods to bring in more cool fresh air to the engine bay and also maybe either contain heat sources or vent/expel the hot air somehow.
Thinking about channeling some cool air to the rear of the engine bay via a front iinlet somewhere and directed towards the rear of the engine, maybe zircotec coating the exhaust headers or cutting some vents into either the bonnet or wings.
Plenty of time for r&d over the winter months however in time for its 'ring debut next year.
Any experiences, mods, tips?
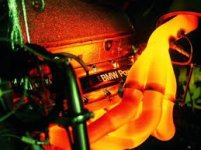
It's obvious that a lot of heat-induced wear&tear, degradation and mechanical failures take place in and around the engine bay of an e85 M54 engined zed and my leaky cam cover gasket is a testament to that fact- it was literally baked hard! I'm keeping an eye on the rearmost 2 coils too as these will be subject to higher temps than the forward ones.
As i plan to get another 100k miles from this car i'm thinking about some minor mods to bring in more cool fresh air to the engine bay and also maybe either contain heat sources or vent/expel the hot air somehow.
Thinking about channeling some cool air to the rear of the engine bay via a front iinlet somewhere and directed towards the rear of the engine, maybe zircotec coating the exhaust headers or cutting some vents into either the bonnet or wings.
Plenty of time for r&d over the winter months however in time for its 'ring debut next year.
Any experiences, mods, tips?
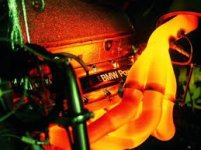