mattyman22
Member
Hey all, I'm new here but I was hoping for a quick assistance to the issue I'm currently having of adding a gps module to my Z4. So I have bought a female connector for the 12v accessory plus in the GPS came with. I've connected the GPS 12v male charger to the female connector and run a wire to a crimped add-a-fuse device with a 10 amp fuse on it. The ground wire is running to a screw just below the glove box which is helping to secure the glove box on the dash. I've tried to power this on a number of ways now:
1. Add a fuse device with 10 amp fuse into an empty fuse slot (F2). Nothing.
2. Add a fuse device connected to an existing 10 amp fuse F6 (with my added on fuse in the second slot). Nothing.
3. I have tested the GPS 12v male connector into the cigarette lighter and it turns right on. So it seems to be operating just fine.
Each time in each of these configurations I have turned the key all the way over and nothing happens with the GPS. I'm lost here!
Could it be a bad ground on that screw? I have tried flipping the way I put the fuses in all different orientations to no success as well. (no blown fuses either).
Gods, help me please!
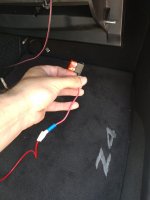
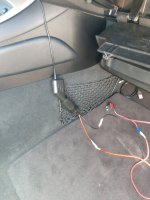
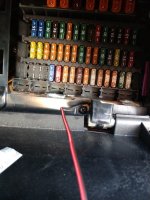
1. Add a fuse device with 10 amp fuse into an empty fuse slot (F2). Nothing.
2. Add a fuse device connected to an existing 10 amp fuse F6 (with my added on fuse in the second slot). Nothing.
3. I have tested the GPS 12v male connector into the cigarette lighter and it turns right on. So it seems to be operating just fine.
Each time in each of these configurations I have turned the key all the way over and nothing happens with the GPS. I'm lost here!
Could it be a bad ground on that screw? I have tried flipping the way I put the fuses in all different orientations to no success as well. (no blown fuses either).
Gods, help me please!

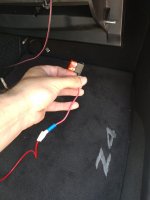
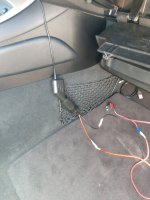
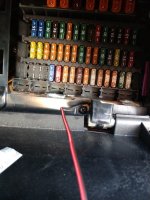